Standard Winches
InterOcean Systems Standard Winches are anything but Standard. Every winch is proudly designed and built in the USA will meet and exceed the exacting requirements of customers like you. All our winches and cable handling systems can be customized with various options.
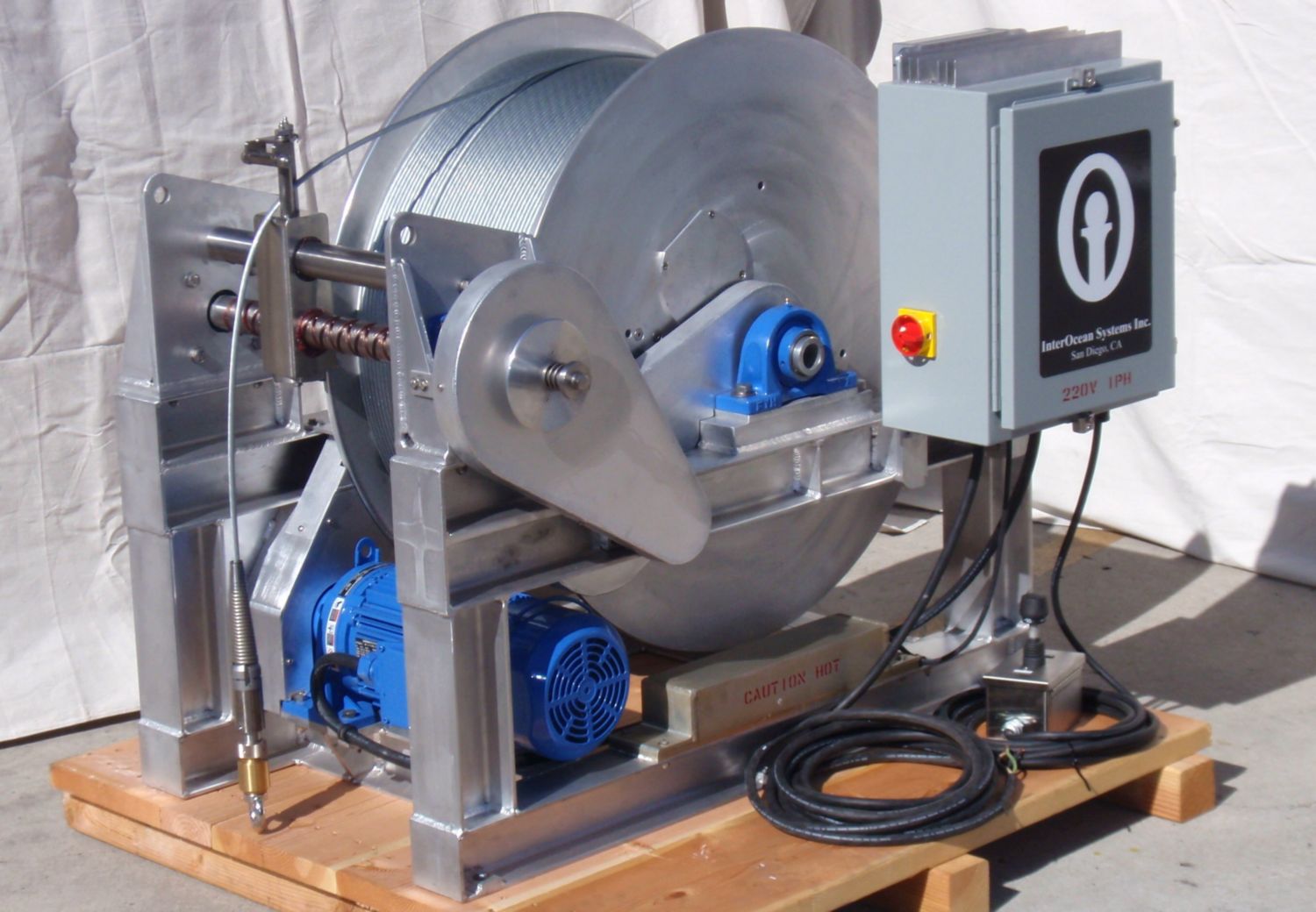
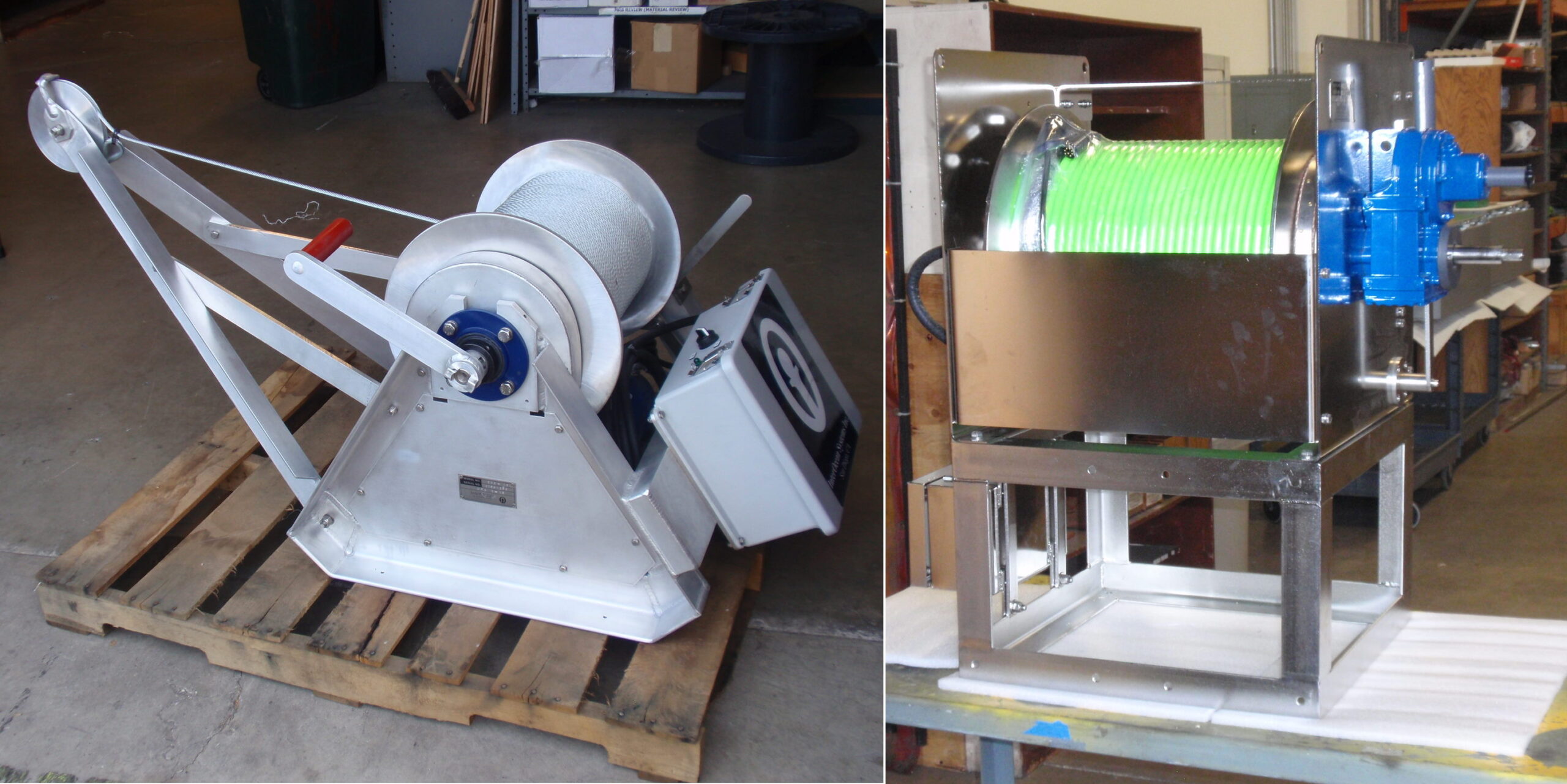
Series 288 & 388
InterOcean Series 288 and 388 are compact electric winches that incorporate 12/24 VDC or 115/220 VAC electric motors with infinitely variable speed control, lightweight materials, and high-quality construction for portability and long-term use on small boats. The Series 288 is our smallest, lightest, and simplest winch for loads up to 500lbs. The Series 388 is a modular designed multi-use winch that is custom configured to meet your demanding requirements. The Series 388 can be upgraded with modular accessories such as an automatic level wind, a mounting flange for optional slip ring assembly for use with any real-time / EM data cable, remote controls, and even an optional boom/sheave/A-frame for over-the-side operations.
Winch Questionnaire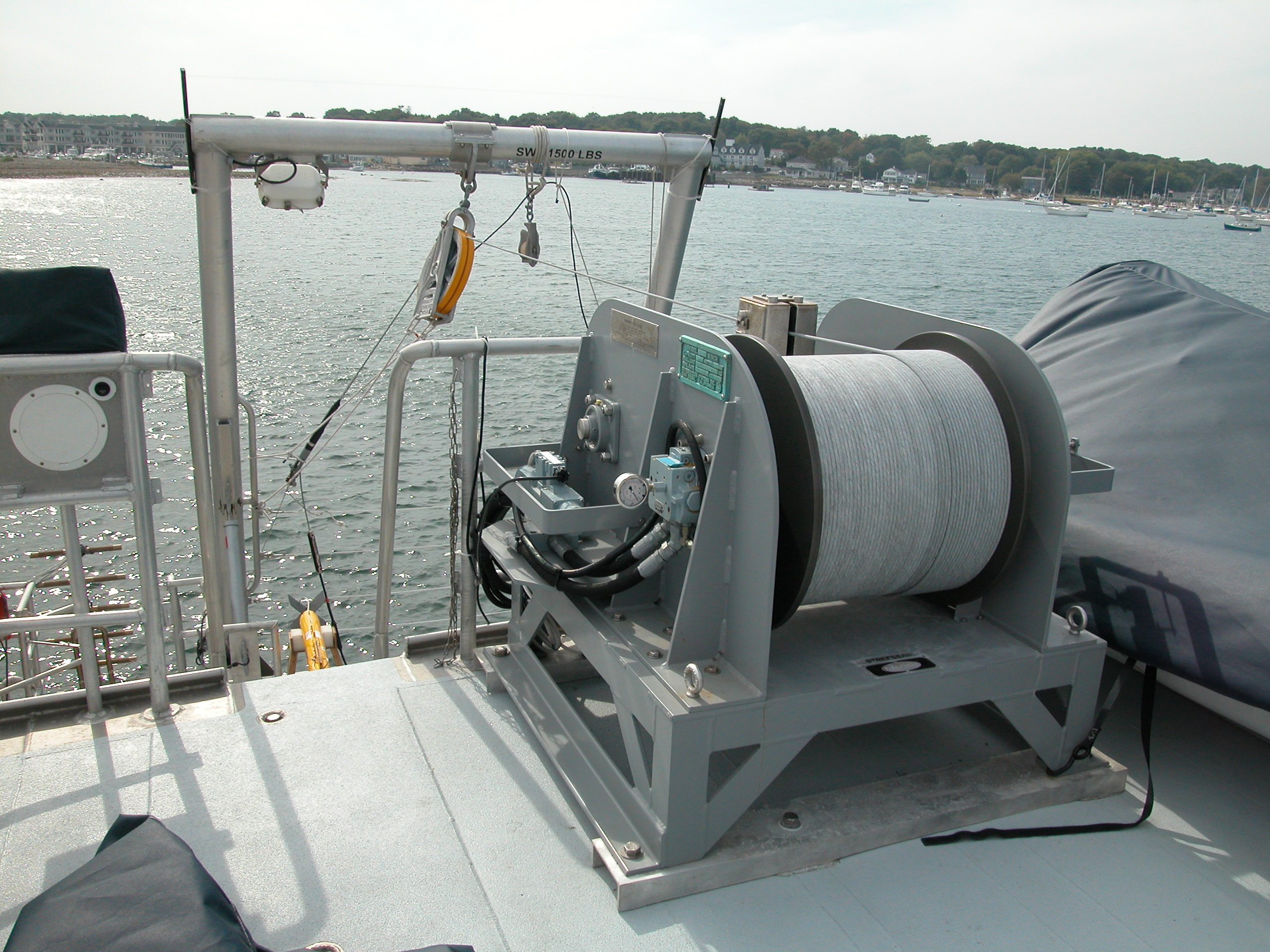
Series 1673
A proven multi-purpose winch often used for hydrographic sampling, CTD, side-scan sonar, and water sampling applications. The Series 1673 is fully self-contained and incorporates an electric or hydraulic motor, generally in the range of 500 to 3,000lbs (2.2 to 13.3 kN) of line tension. The Series 1673 is equipped with an infinitely variable joystick speed control, brake, and level-wind, but which can be customized to suit your needs. The Series 1673 is expertly crafted from lightweight aluminum alloy for portability and long-term use in the marine environment.
Winch Questionnaire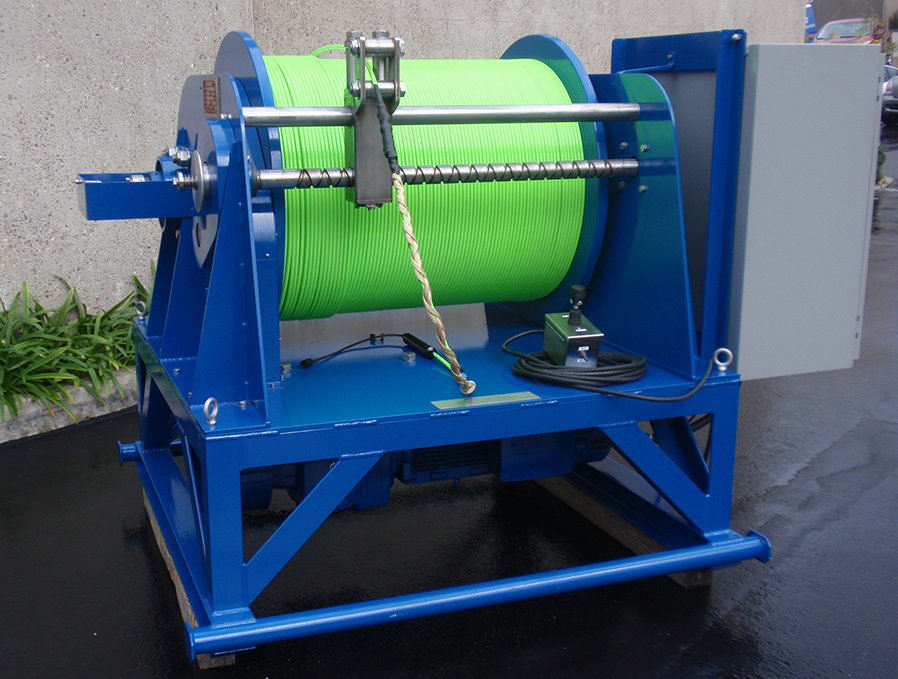
Series 1871
The Series 1871 Medium-Duty Hydrographic Winch for Tow/CTD is a highly versatile medium-duty winch designed to accommodate longer cable lengths for mid-water hydrographic, CTD, and towing applications. The Series 1871 incorporates steel construction for long-term marine operations with high reliability and exceptional utility. The Series 1871 be configured with either electric or hydraulic drive systems for line tensions ranging from 500 to 8,000 lbs (2.2 to 35.6 kN). The Series 1871 incorporates level wind and remote joystick control as standard features. Slip ring, grooved drum, and other options are available.
Winch Questionnaire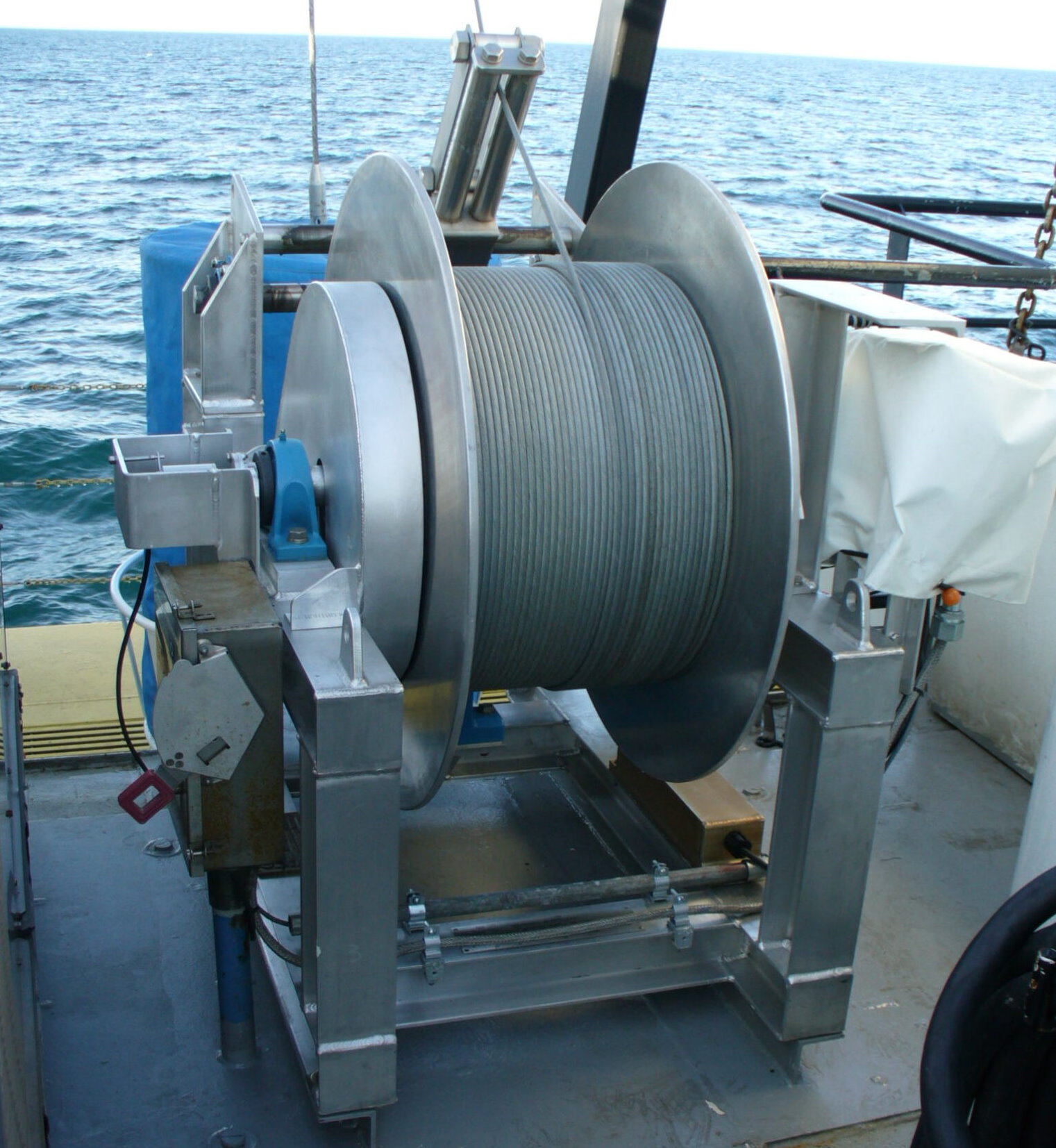
Series 10031
The Series 10031 is a Heavy Duty, Compact Winch with a remarkable capacity for its size. This configuration is ideally suited for handling larger diameter tow cables required by side-scan sonar, sub-bottom profilers, magnetometers, or towed vehicles from small to medium-sized vessels. The Series 10031 is available with level wind, grooved drum, slip ring, and either electric or hydraulic drive systems for line tensions ranging from 500 to over 10,000lbs (2.2 to 44.5kN). Series 10031 winches are generally made from high strength aluminum but can be offered in steel and customized to meet your specific requirements.
Winch Questionnaire